The following are questions asked by busy managers and our answers are short, practical and non-technical. If you think that one of these situations applies to you and you would like more information, please do not hesitate to contact us on 0800 8048564.
Why are pallet trucks noisy on ramps?
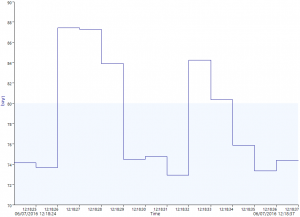
Time history lowered pallet truck

Time history raised pallet truck
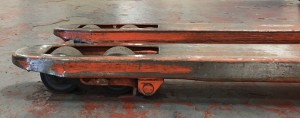
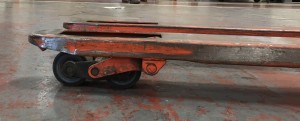
My extraction installer said that the extraction has to be COSHH tested. What is it and who does it?
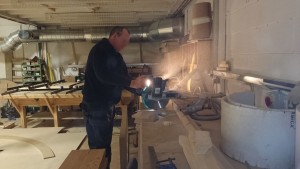
Under the Control of Substances Hazardous to Health Regulations 2002 (as amended 2013) Regulation 9 states that controls have to be maintained, examined and tested. Most systems should undergo “thorough examination and test” every year, at least every 14 months. Extraction removing dust from the abrasion of non-ferrous castings is every 6 months.
The test should be thorough. It should include a check on the physical condition of the plant, measurement of the performance (pressures and flow rates) and confirmation of control of emissions. The test should be performed by a competent person. This will be a professional with a qualification from the British Occupational Hygiene Society; P601, LFOH or MFOH or with an LEV testing “passport” from the Institute of Local Exhaust Ventilation Engineers. Further information can be found on the HSE website. You can find out more about how to look after your LEV on an LEV Awareness course. LK
Is smoke from CNC milling of Duplex worse than oil mist?
The short answer is yes! It is a symptom of a bigger problem.
Smoke means that the coolant is getting too hot and is unlikely to be doing its job properly. If the coolant is correct for the job, then your management of the coolant should be looked at. Poorly managed coolant will contain swarf, dissolved metals, tramp oil and bacteria as well as the neat coolant and water. When inhaled as a mist from the machine, this mixture will cause sore throats, coughs and wheezing. When heated excessively, volatile breakdown products of the oils will enter the air as well, causing further irritation and coughing. Skin exposure will cause dermatitis and possibly sensitisation.
Well managed coolant is less hazardous to health although mist may still cause irritation when breathed in. Management of coolant means the removal of swarf and tramp oil and weekly checks on pH, concentration and bacterial growth. Checks can be performed quite cheaply in-house or the coolant supplier may (is likely to) provide this service. You will need pH paper strips, a refractomer and dip-slides. Further information on coolant management is available from the HSE website or from your coolant supplier. LK
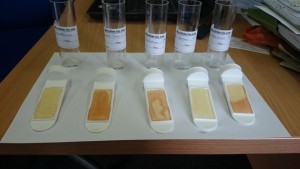
How much RCS silica is in sand?
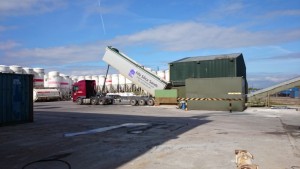
The short answer is; it is definitely there and will cause damage, so does it really matter how much? Take precautions anyway.
Most building and refractory sand is quartz. Quartz is crystalline silica. When sand is agitated and dried, finer grains of sand are made. Grains of sand less than 4 microns in diameter are small enough to enter deep into the lungs where they will cause serious long term damage. This is Respirable Crystalline Silica (RCS). All processed sand will contain RCS. How much is contained is hard to determine accurately. This is only done for the purposes of REACH and labelling.
Regardless of how much RCS is contained in the sand, emissions of fine dust should be prevented using enclosure and extraction, vacuuming rather than sweeping. If a cloud of dust can be seen in a beam of light, a mask should be worn. Processed sand may make up 80% of mortar, concrete and refractory products. Further information on control of RCS may be found on the HSE website.
How can I reduce noise from airline blowing?
The quickest answer is don’t use an airline! Consider alternative cleaning methods, possibly using vacuums for dry debris or brushes for damp/ oily debris.
If you have to use an airline, reduce the pressure, possibly to 2 bar and fit a diffuser onto the air gun. The following are results from an actual survey;
Cleaning Method | Average noise level at the ear LeqdB(A) | Airline noise level dB(A) |
Brush![]()
|
77 | n/a |
Original airline
|
90 | 100+ |
Tool room diffuser on loan
|
84 | 90 – 95 |
How can I tell if I have a noise problem?
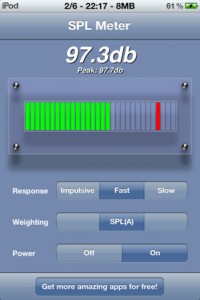
The rule of thumb is whether you can have a normal conversation with someone one meter away.
The Control of Noise at Work Regulations 2005 give two Action Values; one at 80 dB(A) and the other at 85 dB(A). When noise exposure over a shift exceeds the first, hearing protection must be provided and employees should be made aware that noise could damage their hearing. When noise exposure over a shift exceeds the second, hearing protection must be worn and hearing tests must be given. The “conversation at 1m” is around the 80 dB level.
There are many good “sound meter” phone apps available. If this shows that noise levels are above or below 78 dB all the time it would give a good indication of whether or not there is an issue with noise. A quiet workplace with occasional very high noise levels, such as dropping steel, airline blowing or power tool use is likely to have a significant noise problem. If you think your premises have a noise problem, then you should invest in a professional survey from an occupational hygienist or an acoustician.
How can I tell whether the extraction is working?
You need a sensor that will detect pressure or flow and the sensor must be labelled with the range of values within “safe” limits. Your extraction installer will be able to provide such a sensor. It should determine flow in ducting leading to a hood but if this is not feasible, it should show there is flow in a main duct. The gauge must be easily viewed from ground level! For it to be useful rather than ornamental, check it every day. LK
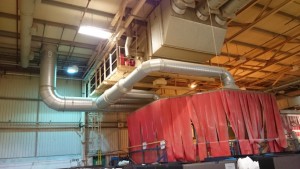
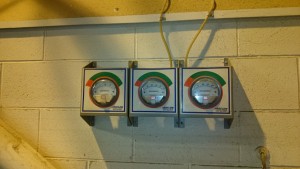
How can I tell if our neighbours are right to complain about our noise?
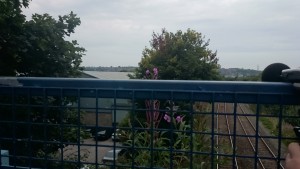
There is a British Standard on this issue BS 4142 which has been recently updated. This is about assessing industrial noise in a mixed residential area.
As a first step, measure the noise at your boundary closest to the neighbours, with the factory running as normal and again at a similar time, with the factory not running. If there is less than a 5 decibel difference, you may have some defence about the complaints. If the difference is above 5 dB, or if the noise from your factory contains clatters and bangs such as from forklift trucks, or a rhythmical noise or squeals from plant, the neighbours are probably right to complain. You can establish this with a regular integrating sound level meter and your own ears.
If the issue is serious and involves litigation or planning permission, a full survey should be commissioned through a consultant with an acoustics qualification and experience of environmental noise surveys. The consultant will be required to use a special noise meter that registers A90 levels (average A weighted noise level for 90% of the time) and they will use sound distribution predictive software which will take wind and cloud cover, buildings and hills and traffic into account. LK
Can our MIG welder claim for industrial deafness even though we gave him ear plugs?
Oh dear. I am afraid he can. Whether your company have to pay all of the compensation or just part of it depends on your records. If it is his fault from loud hobbies, he will receive less compensation. If it can be proved to have arisen from a previous employment, the proportion that you and the previous employer pay will be negotiated.
The following records will reduce the amount you have to pay;
- Pre-employment medical showing that there was existing hearing impairment before he started work with you,
- Audiometry (hearing test) records showing that his hearing impairment had not worsened beyond natural ageing during employment with you,
- Proof that the ear plugs provided were suitable for protection from MIG welding noise; this may be in a noise exposure report or you can test this now. MIG welding can give rise to noise levels between 100 and 110 dB(A) with a high frequency bias. The ear plug manufacturer will be able to advise.
- Proof that you had provided information and training at the start of work, on the risks to hearing and on how to wear ear plugs and you had provided refresher training during employment,
- Proof that you enforced the wearing of hearing protection and checked that it was worn.
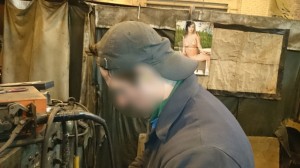